The Important Duty of Container Welding Examination in Ensuring Structural Integrity and Security Compliance in Industrial Applications
In the world of industrial applications, storage tank welding examination arises as a crucial component in securing structural stability and making sure conformity with safety policies. Utilizing a combination of strategies such as aesthetic evaluations and progressed testing approaches, these evaluations serve to identify and mitigate potential imperfections prior to they rise into significant risks.
Value of Storage Tank Welding Examination
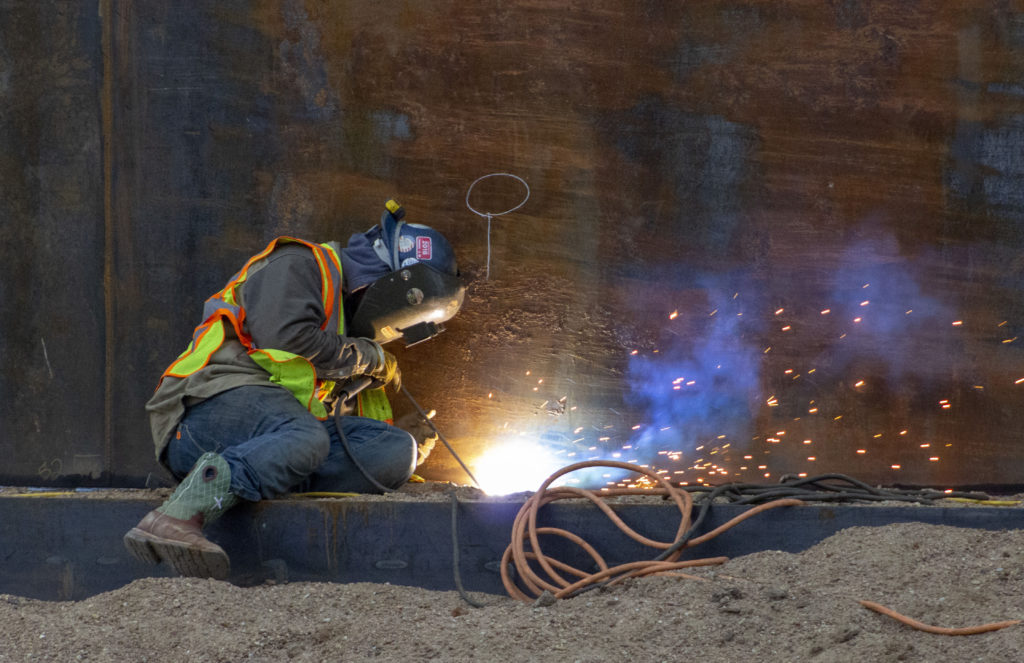
Guaranteeing conformity with market standards and laws is an additional considerable aspect of tank welding inspection. Regulative bodies mandate stringent standards for the building and upkeep of storage space tanks, and complete assessments assist companies stick to these demands. Non-compliance can cause severe penalties, including penalties and closures, further highlighting the need for extensive evaluation methods.
Moreover, storage tank welding examination plays a crucial duty in preserving operational effectiveness. In recap, the significance of tank welding inspection lies in its capacity to protect public health, secure the setting, and ensure compliance with regulative frameworks.
Secret Assessment Techniques
Efficient container welding inspection depends on a variety of key methods that make sure thorough assessment of weld quality and structural stability. Amongst one of the most prevalent methods are visual examination, ultrasonic testing, radiographic testing, and magnetic bit testing - Tank Welding Inspection. Each approach supplies one-of-a-kind advantages in evaluating different facets of the weld
Visual examination offers as the first line of protection, permitting assessors to recognize surface flaws, irregularities, or inconsistencies in the weld grain. Ultrasonic screening uses high-frequency acoustic waves to detect internal imperfections, such as splits or voids, providing an extensive evaluation of weld honesty. This approach is particularly efficient in discovering problems that may not be noticeable on the surface area.
Radiographic screening uses X-rays or gamma rays to produce photos of the welds, revealing internal interruptions and giving a long-term document for future recommendation. This strategy is very efficient for critical applications where the danger of failing need to be decreased.
Finally, magnetic particle testing is utilized to recognize surface area and near-surface defects in ferromagnetic products. By using electromagnetic fields and fine iron fragments, assessors can pinpoint suspensions that could jeopardize the architectural honesty of the container. Together, these strategies form a durable framework for making certain top quality welds in industrial applications.
Conformity With Safety And Security Criteria
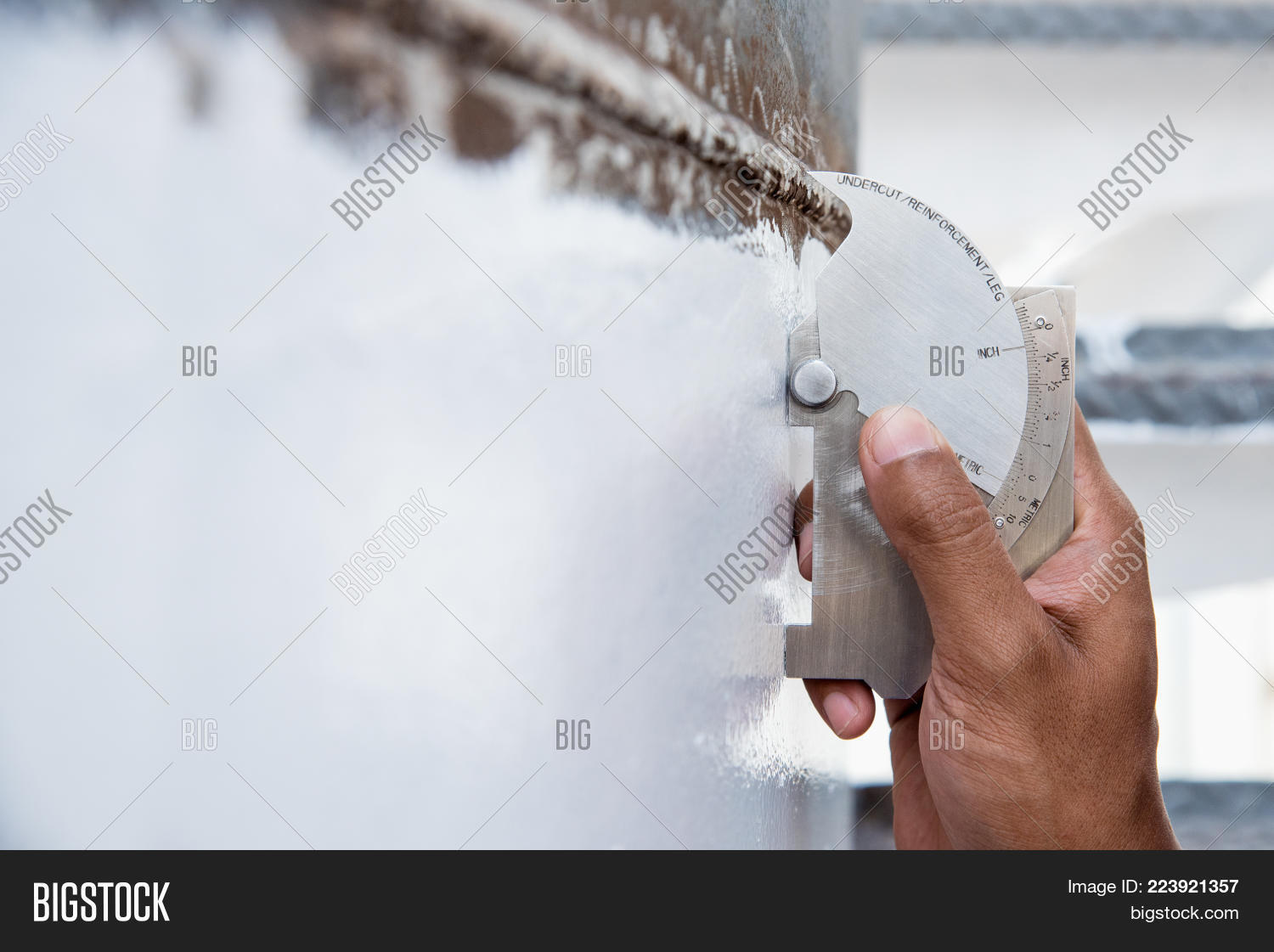
Routine assessments play a crucial role in ensuring compliance by recognizing prospective failures or variances from suggested requirements. Assessors are trained to examine weld high quality, confirm material specifications, and evaluate the overall structural stability of storage tanks. Their knowledge is vital in ensuring that welding processes fulfill the needed security criteria.
Furthermore, compliance with safety and security standards not just safeguards employees however additionally safeguards the setting from possible dangers such as leakages or tragic failings. Organizations that prioritize safety compliance are better placed to minimize risks, boost operational efficiency, and cultivate a society of security within their workforce. In summary, maintaining strenuous conformity with safety requirements is important for the successful operation of storage tank welding tasks in industrial setups.
Advantages of Normal Evaluations
Routine evaluations are integral to maintaining the architectural integrity and security of welded containers. These evaluations supply an organized strategy to determining potential problems or weak points in the welds, making certain that any kind of issues are resolved prior to they rise into significant failures. By conducting normal assessments, companies can spot deterioration, tiredness, and other forms of wear and tear that might compromise storage tank efficiency.
In addition, regular evaluations contribute to conformity with industry policies and standards. Sticking to these guidelines not just reduces lawful risks but also improves the company's online reputation for safety and security and integrity. Normal examinations foster an aggressive security society, encouraging workers to acknowledge and prioritize the significance of devices honesty.

Instance Researches and Real-World Applications
Study and real-world applications highlight the concrete effect of efficient container welding inspection methods. One notable example is a huge petrochemical center that faced significant functional disturbances due to leaks in storage containers. Complying with the execution of rigorous welding assessment protocols, consisting of visual and ultrasonic screening, the center recognized crucial imperfections in weld joints that can have resulted in devastating failures. This positive technique not just stopped ecological dangers yet additionally saved the company millions in prospective cleaning prices and governing penalties.
In a similar way, a water therapy plant carried out a thorough assessment program for its storage tank welding operations - Tank Welding Inspection. By integrating non-destructive screening approaches, the plant was able to find very early indications of corrosion and tiredness in weld joints. This timely treatment expanded the life-span of the tanks and made certain compliance with security laws, hence safeguarding public wellness
These study emphasize the significance of regular and methodical container welding examinations. By prioritizing these practices, industries can reduce threats, boost structural integrity, and ensure compliance with safety and security requirements, eventually resulting in boosted operational efficiency and lowered obligations.

Final Thought
Finally, container welding inspection is an important component of preserving structural stability and security in industrial applications. Utilizing numerous evaluation techniques ensures very early discovery of prospective imperfections, consequently avoiding catastrophic failings. Adherence to security standards even more improves functional dependability and compliance with governing demands. Ultimately, routine evaluations not only safeguard public health and wellness and the environment yet additionally add to the longevity and performance of essential properties, emphasizing the crucial role of this technique in commercial procedures.